Maximizing Value with Condition, Functionality and Capacity Assessment
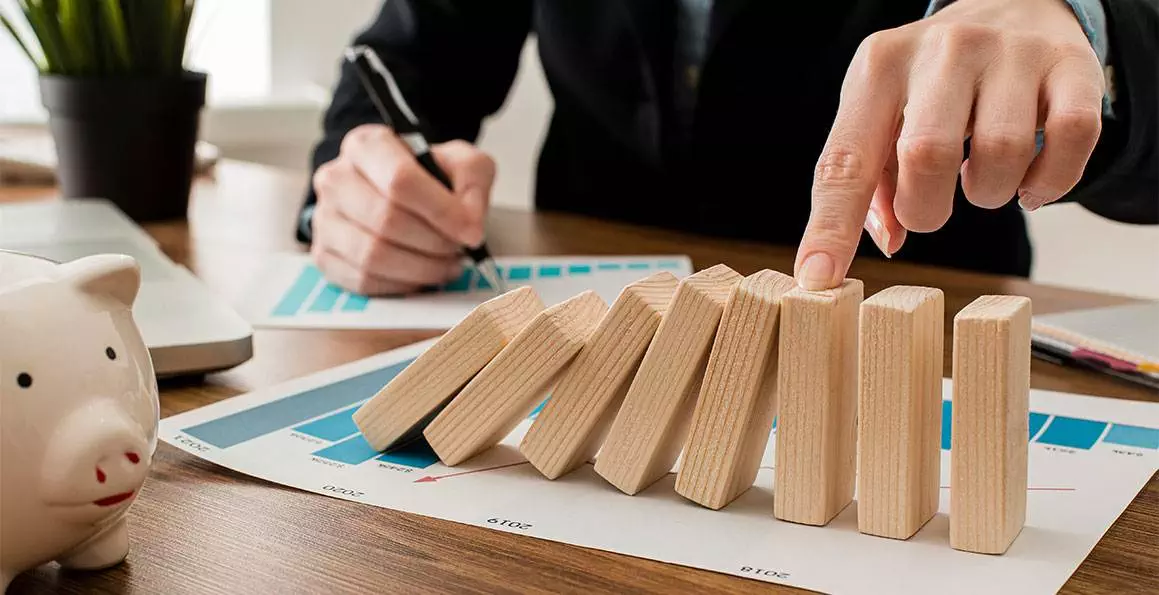
The Physical Assets We Assess
ASI performs on-site condition, functionality, and capacity assessments of various assets, including but not to:
- Electrical Transmission and Distribution Structures: towers, members, poles, foundations, hardware, insulators, dampers, conductors, grounding systems, cathodic protection, hot-dipped galvanizing, and below-ground coating systems.
- Transportation: Highways, roadways, sidewalks, bridges, traffic signals, streetlights, parking lots, parkades, parking meters, guard rails, retaining walls, street signs
- Community/Municipal Facilities: Town halls, fire stations, recreation centres, operations buildings and yards, libraries, courthouses, schools, administration buildings, and transit buildings.
- Parks and Recreation: Trails, benches, shelters, bike racks, basketball courts, tennis courts, baseball diamonds, irrigation systems, bike parks, skateboard parks, playgrounds, gazebos, greenhouses, and docks.
Water Supply and Stormwater - Management: Valves, pumphouses, hydrants, wells, water mains, water distribution services, water meters, reservoirs, water treatment equipment, catch basins, manholes, and stormwater mains.
Condition Assessments: What is the Health of your Assets?
A condition assessment is a detailed visual examination of your assets and systems. The goal is to find any signs of wear, defects, or potential issues that could cause problems down the line. ASI’s engineers and field experts examine each component to evaluate the present condition. This involves both on-site inspections and technical tests to get a complete picture of your asset’s health.
Steps Involved in Condition Assessments
- Visual Inspection: Check the exterior for visible damage, such as rust, cracks, or worn-out parts, and inspect the surroundings for environmental factors.
- Operational Testing: Unusual noises and vibrations and monitor overall performance under normal conditions.
- Technical Analysis: Quantifying damage using tools such as ultrasonic testing and damage/loss measurement to detect issues and deficiencies.
- Data Collection: Recording observations and measurements to track the condition over time and predict future issues.
- Review of Maintenance History: Examining past maintenance records to identify recurring problems and areas needing special attention.
Why are Condition Assessments Important?
- Increasing Reliability: Early identification of problems helps avoid unexpected breakdowns, keeping your production running smoothly.
- Extending Life: Regular inspections and repairs prolong the lifespan of your assets, saving money on replacements.
- Optimizing Performance: Well-maintained assets run more efficiently, boosting productivity and reducing costs of downtown.
What Happens After the Assessment?
Once we complete the condition assessment, we compile all the findings into a detailed engineering report. This report outlines the current state of your assets and highlights any issues found during the inspection. It also includes actionable recommendations for repairs, maintenance, or upgrades.
Functionality Assessments: Are Assets Doing Their Job Right?
A functionality assessment is a detailed evaluation of how well assets and systems are performing their specific jobs. ASI ensures that each component of each asset operates correctly and efficiently, pinpointing inefficiencies and areas for improvement.
Steps Involved in Functionality Assessments
- Operational Testing: While assets are in service, observe their performance during normal operations.
- Performance Metrics: Measuring key performance indicators like output, quality, and efficiency.
- Component Testing: Checking individual parts and components to ensure each is working as intended.
- Process Analysis: Examining the workflow to see if assets are integrated efficiently into the system.
- User Feedback: Gathering insights from operators who work with the assets to identify practical performance issues.
Why are Functionality Assessments Important?
- Identifying Bottlenecks: Helps eliminate slowdowns and inefficiencies.
- Improving Efficiency: Finds areas to fine-tune for better performance.
- Enhancing Quality: Leads to higher quality output and less waste.
- Reducing Costs: Better performance lowers operational costs.
- Ensuring Reliability: Maintains consistent reliability performance.
What Happens After the Assessment?
After the functionality assessment, we provide a report detailing functionality and performance issues and provide recommendations for improvements. This helps you make informed decisions to keep your operations running smoothly and efficiently.
Capacity Assessments: Can They Handle the Load?
A capacity assessment evaluates how well your assets and systems can handle their workload. ASI examines whether your infrastructure and equipment can meet current demands and anticipates future growth, helping you avoid bottlenecks and downtime.
Steps Involved in Capacity Assessments
- Workload Measurement: Assessing the current workload and output of each asset.
- Performance Analysis: Evaluating how well the assets handle peak demands and continuous operation.
- Capacity Testing: Stress-testing scenarios are considered to determine their maximum capabilities.
- Future Demand Forecasting: Predicting future needs based on business growth and trends.
- Efficiency Review: Check if assets operate at optimal capacity and identify any underused resources.
Why are Capacity Assessments Important?
- Preventing Overloads: Ensures assets can handle peak loads without breaking down.
- Planning for Growth: Helps you prepare for future demand increases, avoiding potential bottlenecks.
- Optimizing Resources: Identifies underutilized infrastructure, equipment, and opportunities to redistribute workloads.
- Enhancing Reliability: Ensures consistent performance even under heavy demand, reducing downtime.
- Cost Management: Helps avoid unnecessary investments in new equipment by maximizing the use of existing assets.
What Happens After the Assessment?
After the capacity assessment, we provide a detailed report outlining the asset’s current capacity and recommendations for improvements. This report helps you plan maintenance, upgrades, and future expansions.
What Next?
Documenting the Findings: Engineering Reports
After conducting these assessments, we document all findings in detailed engineering reports. These reports are more than just a collection of data—they provide actionable insights and recommendations.
Wrapping it Up
These three key assessments are the key to keeping your business running smoothly. Asset Strategy Inc. helps you prevent failures, avoid downtime, and reduce life cycle costs by checking your assets’ health, performance, and capabilities.
Condition Assessments of Physical Assets
Condition assessments systematically evaluate an asset’s physical state and performance to ensure reliability, safety, and…
The Importance of Asset Management for Buildings
Building Condition Reports (BCR) and Climate Risk and Vulnerability Assessments (CRVA) are crucial for maintaining structures’ safety…
Experts in Municipal Decarbonization and Energy Reduction Strategies
The push for sustainability has never been more critical, especially for municipalities seeking to lower their carbon footprint…